管材激光切管机处理碳钢穿孔优化及缺陷分析
穿孔的类型不同,缩短时间的方法也不相同。
A 脉冲条件穿孔
在使用脉冲条件进行穿孔时,激光照射为脉冲式,此时只有激光照射时的熔融、蒸发与停止时的冷却搭配得好,才能获得良好效果。如果只偏重于提高熔融和蒸发作用,则很容易引起过烧;而如果仅注意增强冷却作用,则穿孔时间又会变长。
B CW条件穿孔
CW 穿孔时会引发一种过烧现象。CW穿孔的优点是可以缩短穿孔时间,但随着板厚的增加,熔融范围将会不断扩大,从而影响加工质量。
C 根据穿孔的进展状况来调整条件
在穿孔加工中,当激光束的照射量过大或过小时,应边观察加工情况,边调节条件,直到将条件调整到最优为止。
【原因与对策】
A 脉冲模式穿孔
要提高熔融能力和冷却能力,就需要在短时间内照射大量的能量,并能同时确保照射后的冷却时间。
如图3.2-1和图3.2-2所示,高峰值的矩形脉冲波形的脉冲式照射的效果最为理想。熔化所需能量以强度E与照射时间T的乘积来表示。三角波与矩形波脉冲相比,要得到同等的能量,三角波脉冲所需照射时间为矩形波脉冲的2倍,结果就是输入到被加工物内的热量增加,容易引起过烧。
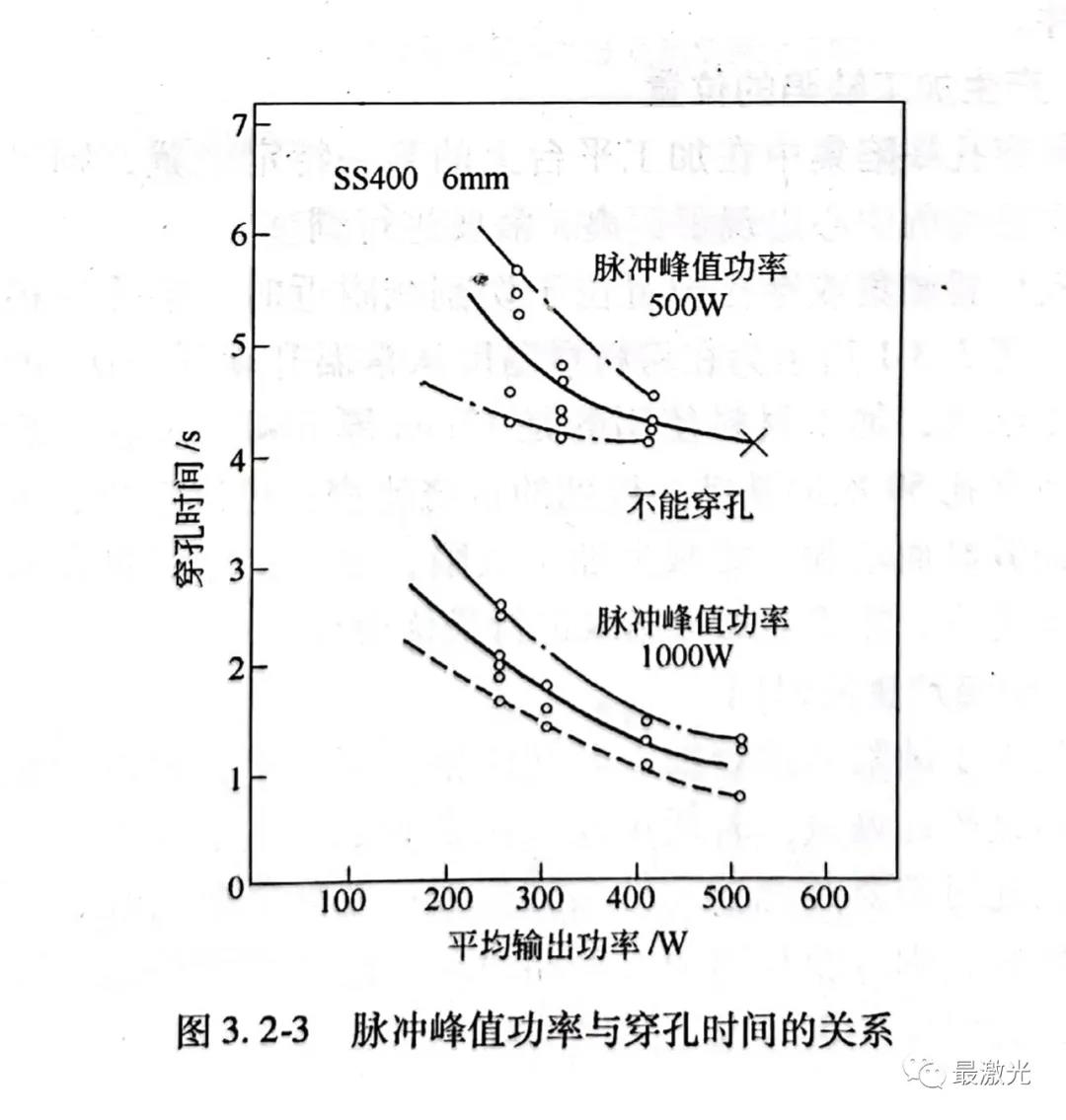
图3.2-3所示为在6mm厚SS400材料切割中所表现出来的脉冲峰值功率与脉冲平均功率效果,脉冲峰值功率越高,穿孔的时间越短。
B CW模式穿孔
板厚超过12mm时,喷嘴要尽量选择小口径的。在重视切割面质量的厚板切割中,则需对穿孔用喷嘴与切割用喷嘴分别进行选择。
C 根据穿孔的进展情况来调整条件
调整条件时,可通过传感器观察穿孔部分熔融状态的辉度,当熔融范围有扩大倾向时,就降低激光的强度;反之,当熔融作用下降时,就加强激光的强度,最终达到小孔径高速穿孔的目的。
解决穿孔缺陷的方法
【现象】
造成穿孔缺陷的主要因素包括:发生的瞬间、发生的位置、发生的时间及其材料本身因素。请参照表3.3-1来对主要因素进行分析。
【原因与对策】
A 产生缺陷的瞬间
需要确认缺陷是在何时产生的,是发生在穿孔的中途,还是在穿孔过后刚刚开始切割时。如果是产生在穿孔的中途,则要看是产生在刚刚开始穿孔时,还是产生在向其他条件切换时,然后再根据情况进行相应的调整。如果缺陷是产生在穿孔就要结束时,则原因就在于条件在孔还未被穿透时就由穿孔条件变成了切割条件,此时需要延长穿孔时间;而如果是出现在刚刚开始切割时,则是由于穿孔部周围的堆积物使切割变得不稳定,此时需要在开始切割处设置脉冲条件。
B 产生加工缺陷的位置
如果穿孔缺陷集中在加工平台上的某一特定位置,则可能是因为激光和喷嘴的中心出现了偏离,需要进行调整。穿孔位置密集或穿孔位置位于切割线附近时,穿孔处很容易处于高温。
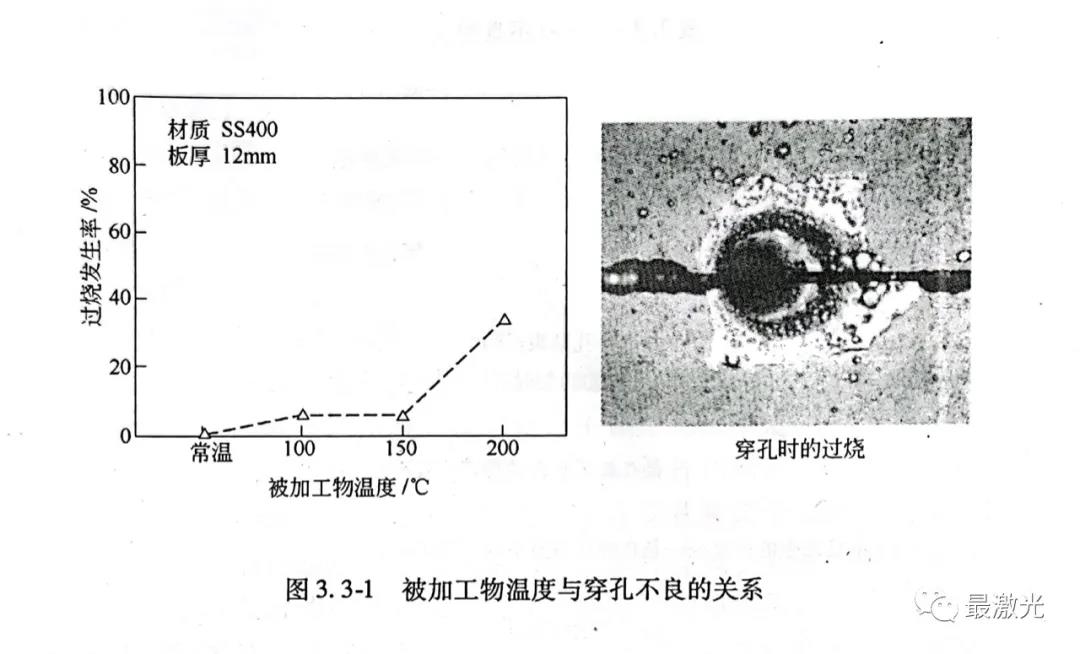
图3.3-1所示为在将材料温度从常温升高到200℃时各温度下的加工结果,加工材料使用的是12mm厚SS400材料。数据是在各温度下穿孔50次的基础上得到的过烧比率。可以看出,加工缺陷随温度的升高而增加。要减少加工缺陷,加工就应尽量在材料的冷却状态下进行,需要对加工路线进行最优设计。
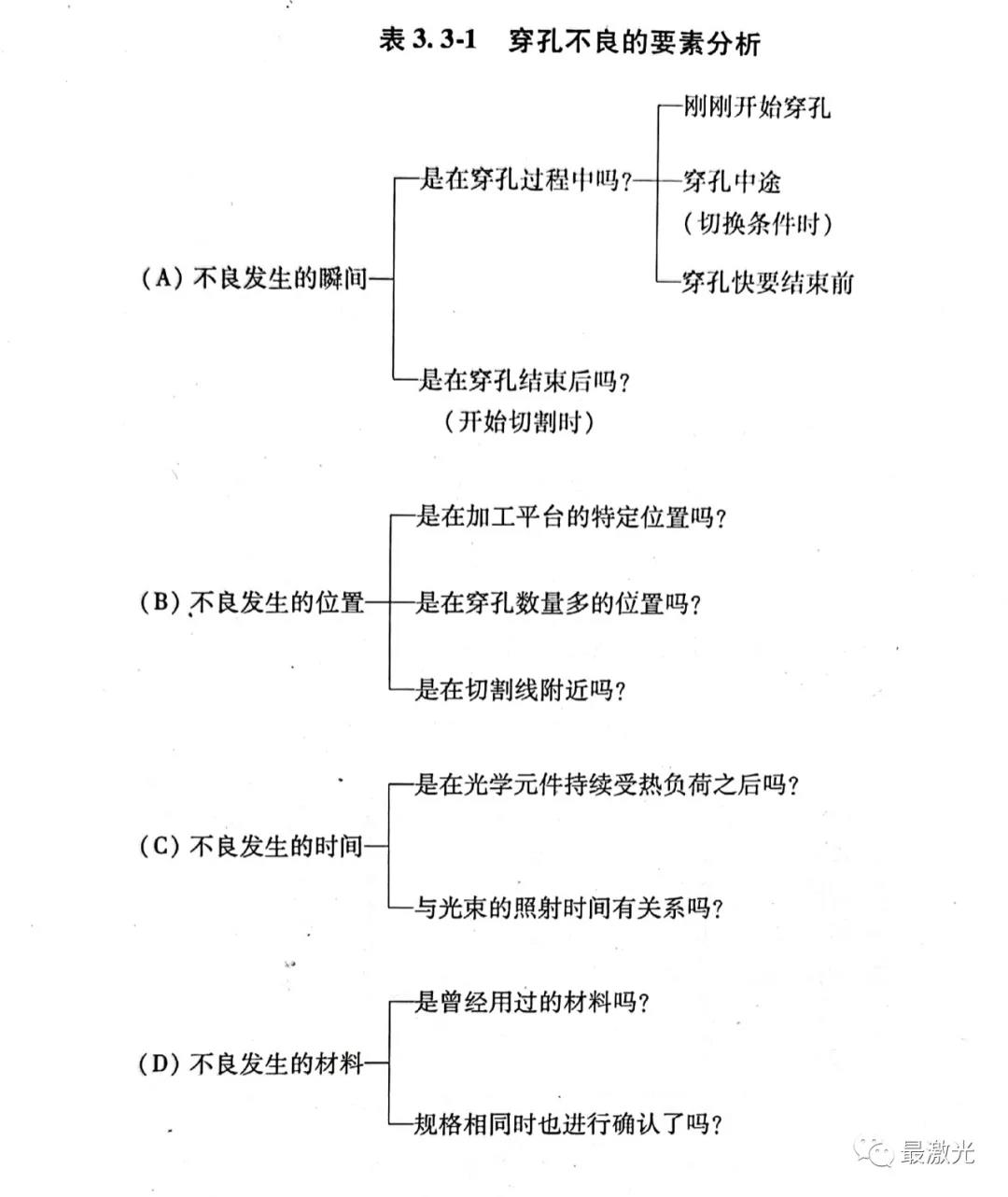
C 缺陷产生的时间
如果加工缺陷是随着加工时间的推移而增多,则再观察增加冷却时间后是否能恢复。若能恢复,就说明是发生了光学元件的热透镜效应,此时需要对光学元件实施保养;而如果是增加了冷却时间也不能恢复,则可能是因为发振器出现了故障导致输出功率产生变动而致,此时应与售后服务部门联系。
D产生加工缺陷的材料
判断缺陷产生的原因是否来自材料时,首先是要查看该材料是否使用过。如果曾经使用过,则不需要再对加工条件进行调整,因为缺陷原因很可能是加工机或光学元件出现了故障。
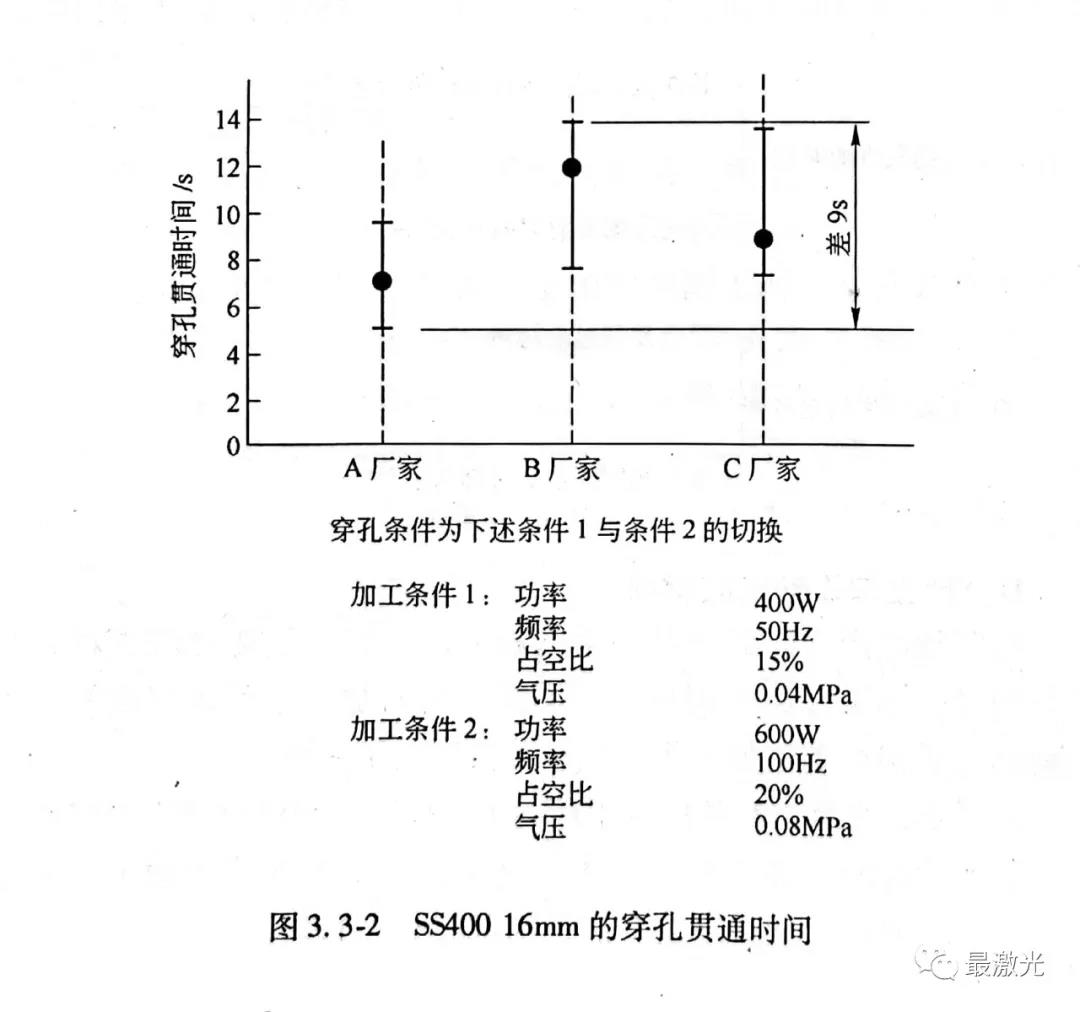
图3.3-2所示为对各厂家生产的16mm 厚SS400材料进行穿孔时的贯通所用时间。如果材质发生了变化,则需要在连续加工前对穿孔时间进行确认,或者对整个加工时间进行稍长设定。